A Look Into The Nickel Mining Process
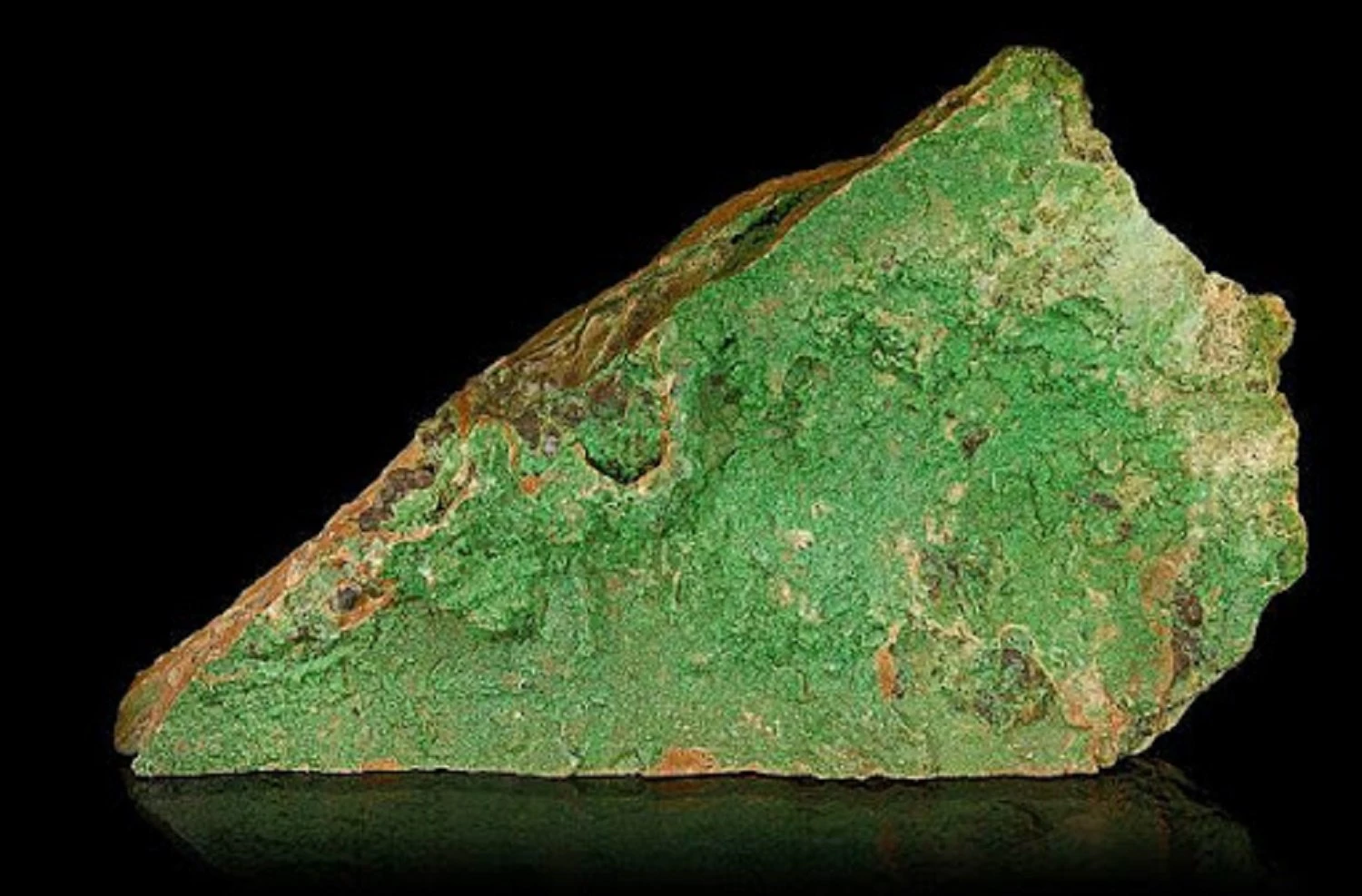
When it comes to metals, Nickel plays a crucial role in human life. Nickel is used in surprisingly numerous contexts, ranging from the mundane to the extremely commercial. Which shows how crucial Nickel mining is and how it affects our lives.
The mining industry has come a long way from its nascent technological beginnings, allowing for a massive increase in Nickel output. The efficiency in types of mining and output of the mining industry have benefited from the development of compact machinery that is both cost-effective and durable. The elimination of waste and potentially harmful substances in the mining process is just one advantage of this development.
An estimated eighty percent of the United States' main (not recycled) Nickel use went toward alloys like stainless steel and superalloys. Nickel improves an alloy's corrosion resistance and high temperature stability, making it ideal for usage in chemical plants, petroleum refineries, jet engines, power generation facilities, and offshore installations. Stainless steel's ease of cleaning and sterilization has made it a popular material for usage in a wide variety of applications, including medical tools, kitchen appliances, and tableware. All United States coins in circulation are constructed of Nickel-based alloys with the exception of the penny. Nickel alloys are becoming the material of choice for rechargeable batteries in electronics, power equipment, and hybrid and electric vehicles. Items like bathroom fixtures get a Nickel plating to protect them from corrosion and improve their aesthetics.
The Philippines comes in second for Nickel production after world leader Indonesia. Estimates put the total amount of the metal in storage at 94 million tons, with the largest reserves being in Indonesia and Australia.
Large quantities of Nickel, estimated at over 290 million tons, may also be present in the metallic nodules that can be found at higher depths of the ocean. These can't be reached until deep-sea methods of mining technology has advanced sufficiently to reach them. Global primary or fresh Nickel mining process production exceeds 1.4 million metric tons per year. 800 million tons of steel and 10 million tons of copper are equivalent to this amount.
In light of the fact that Nickel may be found in two quite distinct ores, it should come as no surprise that their respective mining procedures also vary. Sulfide deposits are often extracted using subterranean methods that are analogous to those used to extract copper. Nickel-rich strata are excavated using giant shovels, draglines, or front-end loaders, and the resulting boulders and debris are dumped.
The mining process of extracting Nickel from its ore is analogous to that of extracting copper, down to the use of some of the same tools and techniques. Most noticeably different is the increased need for cooling to account for the higher operating temperatures inherent in Nickel production, as well as the usage of higher-temperature refractories. When working with sulfide ores versus laterite ores, various processes are employed for each. Sulfides get some of their smelting heat from oxygen reacting with the iron and sulfur in the ore, which is why this type of ore is so difficult to smelt. However, oxide ores do not produce the same reaction temperatures and hence require alternative energy sources for smelting.
The methods of mining Nickel minerals from sulfide ores, they must first be crushed and milled into a fine powder. The ore is stirred with mechanical and pneumatic devices that release air bubbles, and then mixed with specific reagents. Concentrate containing between 6 and 12 percent Nickel is collected as these ascend through the mixture and attract the sulfide particles to their surfaces. A second cleaning process is often applied to the tailings before they are finally disposed. Magnetic separators can be employed in place of or in addition to flotation since some Nickel-bearing sulfides are magnetic.
Although laterite Nickel deposits do not contribute to the pollution problem that sulfide ores do, their mining process can have negative effects on the environment due to the high energy input required (e.g., soil erosion) in mining practices. Because of its composition, the ore constrains the available processing methods. Since laterites are oxides, they cannot be concentrated using the usual methods; instead, massive amounts must be melted down. In addition, they have a lot of water in them, both as moisture and chemically bonded hydroxides (in the range of 35 to 40 percent). Dehumidification and the elimination of the chemically bound water are, thus, significant tasks for the Nickel manufacturer. Large rotary-kiln furnaces are used for these processes. Reduction kilns need to be 5–6 meters in diameter and longer than 100 meters in length to accommodate the enormous tonnages of ore and the requisite retention period. Dryers of this size (50 m in length and 5.5 m in diameter) are popular.
After lateritic or sulfidic ore is extracted and processed, a matte containing Nickel is the byproduct. It is possible to obtain a Nickel that is 95% pure with further purification using the fluid bed roasting process.
Refining can be done faster and more effectively in mining practices with the help of electric cells. Electrical cells with inert cathodes eliminate the final traces of impurities from the Nickel, leaving behind just pure metal. This level of polish is quickly becoming the standard in the business world of mining practices.
Hallmark Mining Corporation is a Nickel manufacturer and mining interest in the Philippines with a commitment to sustainable and responsible mining; for more information visit our website.