A Look Into Nickel Alloy Production
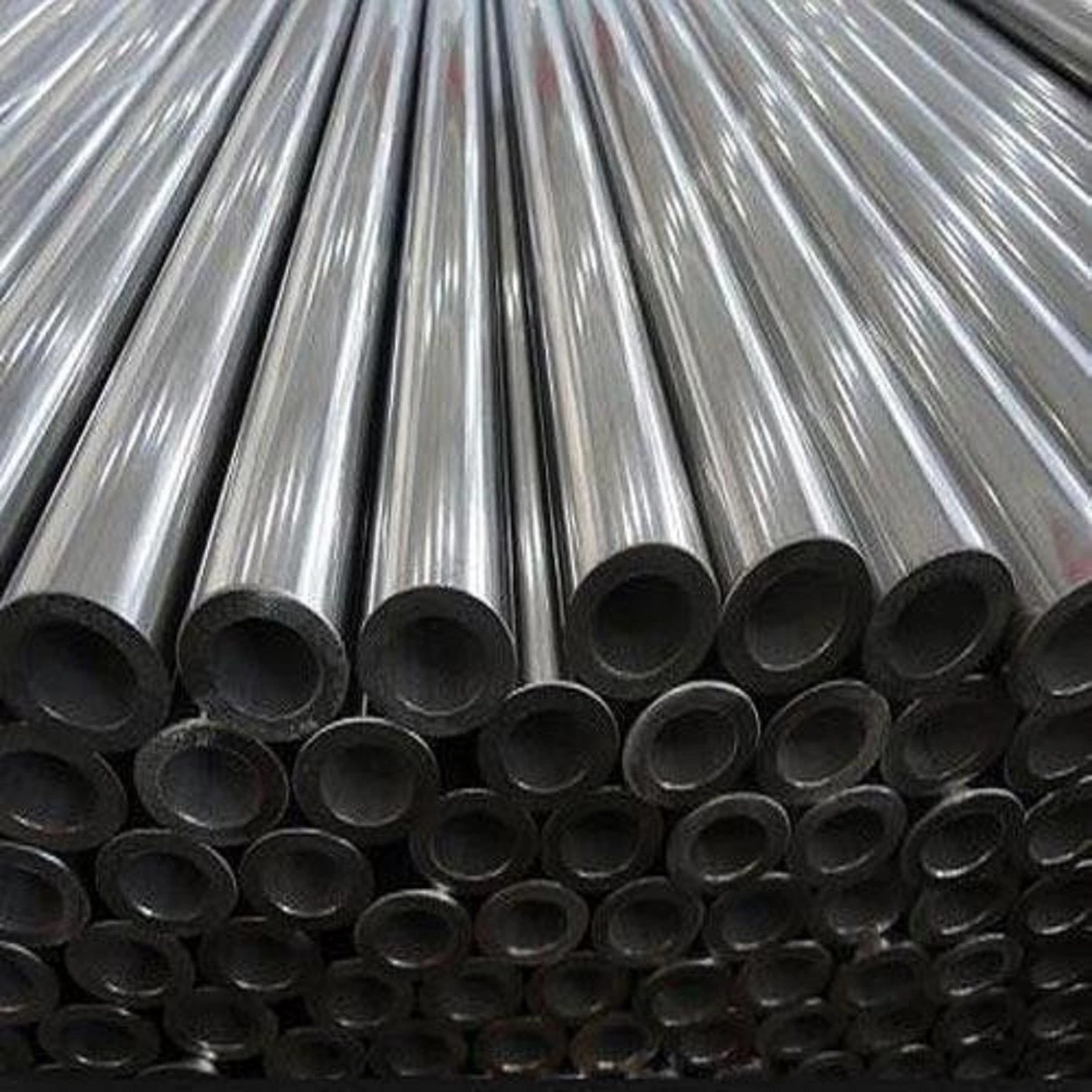
Pure Nickel has a useful combination of properties including corrosion resistance, good strength and high ductility even at extremely low temperatures. It also has useful electronic properties and exceptional magnetic properties. Nickel content is a particularly effective catalyst for the hydrogenation of unsaturated compounds in vegetable, animal and fish oils, converting them from a liquid to a solid. As a result, processed natural oils are used in products such as shortening, oleomargarine, and soap.
Nickel is essential to underpin the oxide-coated cathode used in all television tubes and in all the largest radio power tubes. Alloyed with about 2% tungsten and trace amounts of magnesium, the Nickel used as the cathode base in amplifiers for underground cables is expected to go unnoticed for 20 years.
Nickel is also an essential component of white gold alloys widely used for jewelry. These Nickel-containing alloy
also contain copper and zinc, all of which are of high purity.
The white color of Nickel is very attractive, and most of its alloys with copper are noticeably white. Its ability to form strong and ductile alloys with many metals, including iron, chromium, cobalt, copper and gold, is used in industry.
Nickel-containing alloy are formed by combining Nickel with other metals, usually titanium, copper, aluminum, iron, and chromium. About 3,000 Nickel base alloys are used, forming products for many industries. About 90% of all new Nickel sold each year is used to create alloys. The most common Nickel alloy steels is stainless steel, which accounts for about two-thirds of newly produced Nickel-containing alloys.
To create Nickel alloy steels, start with the purest raw materials available to achieve the required chemical composition. The correct chemical composition is necessary to provide the uniform properties and is required for different alloys. The alloys are then melted, hot rolled and processed to the final size using modern technology.
There are numerous benefits that are found in a Nickel-containing alloy including:
Improved flexibility
Outstanding durability
Increased corrosion resistance
Anti-Oxidant Ability
Improved resistance to higher and lower temperatures
Attractiveness
Electronic properties
Many Nickel-based alloys provide outstanding performance at temperatures above 1000°C, making them well suited for extremely harsh environments. They provide excellent oxidation resistance at high temperatures while maintaining weld quality, workability and ductility.
Nickel-containing alloy have an average life of 25 to 35 years and can extend further depending on the application. With its extended service life, this material is more cost-effective than other metals. Nickel alloys are recyclable and are among the most recycled materials in the world. About half of the Nickel in stainless steel products comes from recycled Nickel feedstock. This material is common in a variety of devices and items that people use every day. Examples include:
Mobile phones
Food preparation equipment
Medical equipment
Laboratory equipment
Transport and Aviation
Medicine
Building materials
Gas and electric turbines
Nuclear systems
There are also numerous industries that benefit from Nickel-containing alloy manufacturing. Industries such as electric power, chemical, petrochemical and energy depend on Nickel superalloys, which have outstanding oxidation resistance and high temperature strength, in critical applications. Nickel, chromium and molybdenum alloys provide better corrosion resistance.
Superalloys are made by adding a balanced amount of elements including chromium, aluminum, cobalt and titanium to create optimal monocrystalline or monocrystalline structures, giving the material greater strength than steel. normally. These Nickel-based alloys are used in extremely hot environments such as gas turbines for power generation and aircraft. Nickel alloys consisting of iron are common in electronics and special engineering. Nickel-copper alloys are used in marine engineering because of their anti-corrosion properties in seawater. The engineering market accounted for 27% of all final applications of Nickel in 2015.
Sewage systems and plumbing have increased their use of this stainless steel because it offers very low rates of corrosion when treating water, even at high flow rates. It also offers incredible strength and ductility as well as ease of fabrication, making it easier to use less expensive joining methods when joining pipes.
Nickel alloys readily with many other metals, including chromium, iron, molybdenum, and copper. This results in a wide range of alloys with exceptional high temperature corrosion and scaling resistance, exceptional high temperature strength and other unique properties, such as shape memory and coefficient of expansion.
Some alloying materials include but are not limited to: chromium, cobalt, copper, and iron. The most common alloy of Nickel is stainless steel. It‘s mainly made up of iron, 18 percent chromium, and 8 percent Nickel.
Nickel alloys can be classified into the following categories namely:
Nickel-titanium alloys
Nickel-chromium-cobalt alloys
Nickel-chromium-molybdenum alloys
Nickel-chromium-iron alloys
Nickel-chromium alloys
Nickel-molybdenum alloys
Nickel-copper alloys
Nickel-iron alloys
Wrought Nickel
Nickel is 100% recyclable and is widely used in the energy, communications, marine, oil and gas and medical industries, but it has its downsides. The most obvious drawback is that mining is the only way to obtain Nickel ore, which is harmful to the environment. In addition, extracting Nickel from laterite ore is expensive because a large amount of energy is required for drying and smelting. However, Nickel and Nickel alloy steels are still an integral part of human civilization, as products made from these substances are very durable and can last for decades.
Hallmark Mining Corporation is a Nickel manufacturer and mining interest in the Philippines with a commitment to sustainable and responsible mining; for more information visit our website.