Nickel Mining Manufacturers Are Working On the Future of Mining Technology
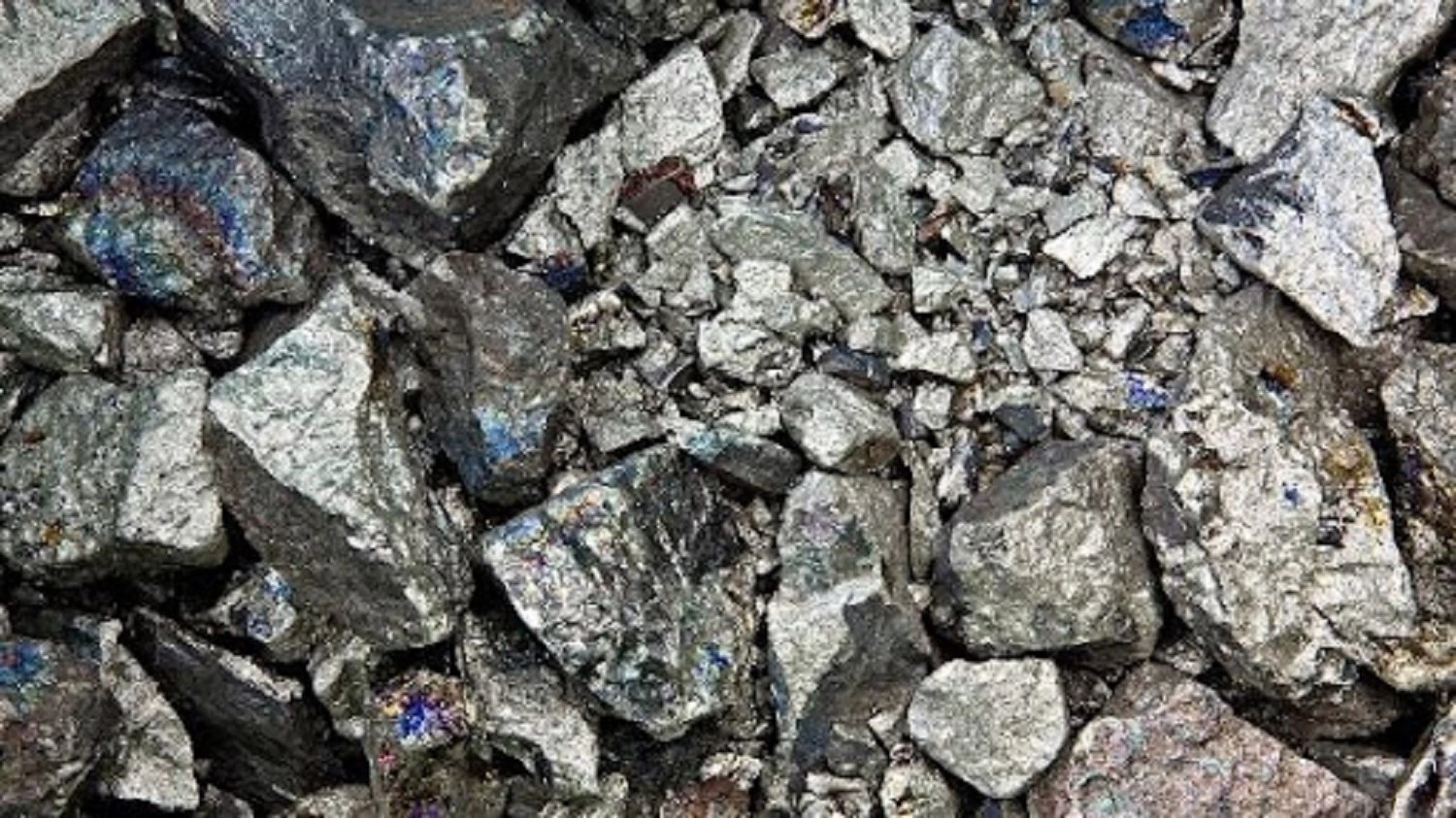
There are two headlines driving mining innovation and the future of mining. Digitization and sustainability. Planning and designing a zero carbon footprint, fully digitally connected mine is the dream goal most mining companies around the world hope to achieve.
Increasing social and environmental requirements mean that miners are applying sustainable, safer, cleaner and more efficient processes. The carbon footprint of mines is enormous and includes many energy-intensive functions. From trucks, excavators and generators to transporting products and waste from mines, our reliance on diesel as the primary source of power for machinery has led to high CO2 emissions. On-site methods such as leaching and recycling strive to produce no waste, but still produce small amounts. Further research is being carried out to bring near-zero waste to zero, in relation to the necessary technological advances, in particular improving permeability and managing the hydrogeology of the mine.
Mining technology and innovation is a long and uphill process, but there are promising prospects already on the horizon. One such mineral processing innovation is from Australian technology company Direct Nickel Limited (DNi) who has partnered with CISRO scientists in Perth to develop an economically viable method of extracting Nickel from low-grade ores.
The project has the potential to impact the mineral processing industry internationally, resulting in the potential for billions of dollars worth of Nickel to be processed.
As traditional sulfate orebodies are being depleted, the focus is shifting to laterite and saprolite ores, which contain about 70% of the world's Nickel. Developing the new extraction technology took him six years after DNi filed a patent for nitric acid recycling. At the same time, the company approached CISRO to cooperate in developing methods for metallurgical processes. A process developed by DNi and CISRO replaces sulfuric acid with nitric acid in high pressure acid leaching. Nitric acid, unlike sulfuric acid, is much cheaper as it eliminates the problems associated with waste disposal and disposal.
Additionally, nitric acid is much more aggressive than sulfuric acid, so Nickel can be extracted at much lower pressures and temperatures, eliminating the need for expensive titanium-lined equipment.
From small-scale testing, the project has evolved into his $5 million pilot plant, capable of recovering 95% of the reagents for reuse, reducing operating costs while removing Nickel and cobalt from deposits. Most can be extracted.
The fact that the acid can be recovered and recycled is a big plus for both sides as it eliminates the high cost of sulfuric acid plants. Neutralization of acid waste. CISRO Perth spokesman Dave Robinson said: There are huge orebodies that are too expensive for current sulfated cutoff grades. ”
According to Robinson, current plants such as Murrin Murrin (NE Goldfields) process about 1% Nickel. “If the cutoff grade can be get down to 0.7 or 0.75, then there will be the potential to process billions of dollars worth of Nickel,” he says.
Environmental benefits
This process not only means that Nickel recovery from low-grade ores becomes an economically viable option. It can also be an environmentally sustainable option. During the process all NOx gases are captured and converted to reusable nitric acid. All leach residues consist mainly of silicates with a low residual nitrate content. In addition, nitrates caused by residues are broken down into nitrogen that can be used for plant growth, returning to the natural nitrogen cycle.
The production of salable magnesia solves the magnesium disposal problem facing HPAL operations. DNi says the amount of waste residue is less than half that of his HPAL process because it requires minimal waste of reagents and neutralizers and produces salable by-products. This is a great advantage in tropical environments with high rainfall.
“In summary, [the process] is a highly efficient and elegant solution to the global Nickel supply problem,” he says DNi.
As Robinson concludes, "Australia can change the value of what lies on the ground."
The next phase of the project is to build a 30,000 tonnes per year Nickel plant to demonstrate full-scale production, and DNi is currently seeking partners to develop such a plant. CISRO has confirmed that it will continue to develop extraction processes for a wide range of applications in the mining industry.
What this means for miners such as Hallmark Mining.
For the Nickel mining company, innovations that bring about more efficient, sustainable, and productive outcomes are always a boon. Mineral processing also has a large environmental impact, thus any mining technology that can ease or remove impacts against the environment also have the benefit of providing a leverage for the Nickel mining manufacturer to engage with local and national authorities.
Hallmark Mining Corporation is committed to sustainable and responsible mining; as a Nickel mining company it is always vigilant of any mining innovation that can give a positive impact on its profit while providing the best possible benefits for its partner communities and its area of operation. For more information visit our website.
Source: Mining Digital