Nickel Batteries, Recycling, and The Challenges Facing Electric Car Companies
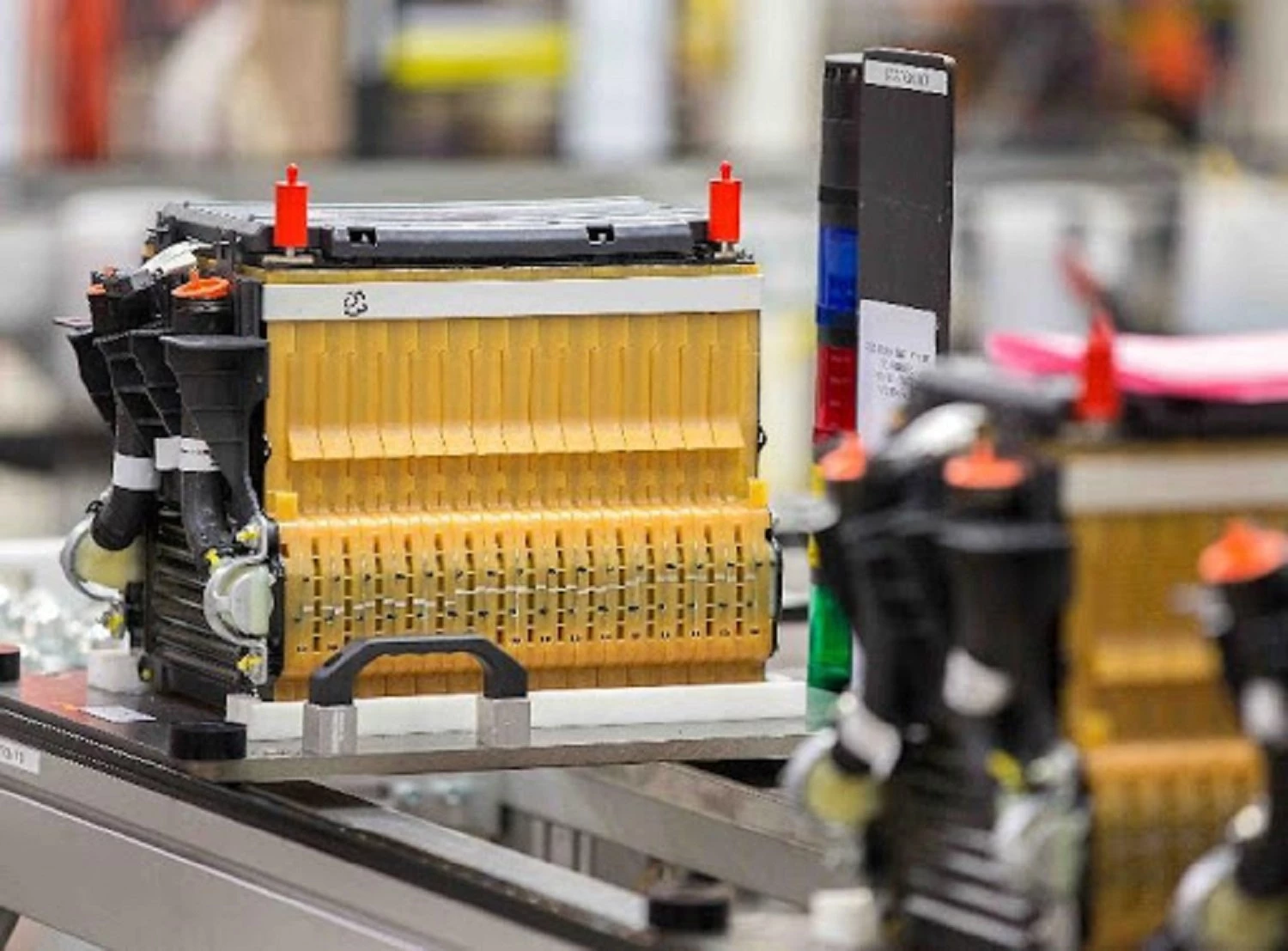
There's been a lot of talk about the electric vehicle market in the auto industry lately, and for good reason. Electric cars are better than petrol cars because they save energy, they allow consumers to reduce their carbon footprint and have a positive impact on the environment. In fact, in October 2018, the delivery of an electric car to its millionth customer took place in the United States, a milestone many expected to take even longer.
But what are these electric cars, how long do electric cars take to charge and can you go to any showroom and buy one? The answer may surprise you. There are currently about forty different types of electric vehicles, from about twenty different electric car manufacturers. These include 100% electric BEV (battery electric vehicle) and PHEV (plug-in hybrid electric vehicle) with battery and electric motor but also internal combustion engine. PHEVs sometimes run on electricity and run on gasoline or diesel when the battery is dead.
Two chemistries of lithium ion batteries dominate electric vehicle batteries – Nickel-Manganese-Cobalt “NMC” and Nickel-Cobalt-Aluminum “NCA”. As between the two chemistries, NMC is used by nearly every automobile maker in the world save it for Tesla. For at least the next decade, the evolution of the lithium ion battery and its NMC chemistry is towards a more nickel rich cathode.
Nickel (Ni) has long been widely used in batteries, with the uses of nickel most commonly in nickel-cadmium (NiCd) batteries and longer-life nickel-metal hydride (NiMH) rechargeable batteries, which have appeared in the years. 1980. They were used in power tools and early digital cameras revealed the potential of mobile devices, changing expectations about the way we work and live. The mid-1990s saw significant use of the first NiMH batteries by electric car companies in the Toyota Prius. Around the same time, the first commercial applications of the uses of nickel through Li-ion batteries appeared, first in camcorders and eventually finding their way into smartphones, laptops, and many mobile devices. another move that we currently own.
The main benefit of uses of nickel in batteries is that it can provide higher energy density and greater storage capacity at a lower cost. New advances in nickel battery technology mean they are set to play an increasing role in energy storage systems, helping to make the cost per kWh of storage batteries more competitive. New nickel-containing battery technology is also playing a role in energy storage systems linked to renewable energy sources. Wind turbines or solar panels generate electricity when the wind or sun is available; modern battery technology allows this energy to be stored for use as and when required.
Nickel metal hydride batteries, commonly used in computers and medical equipment, provide reasonably specific power and specific electrical capacity. Nickel metal hydride batteries have a much longer cycle life than lead-acid batteries and are safe and resistant to abuse. These batteries have been widely used by electric vehicle companies in their hybrid electric vehicles. The main challenges of nickel-metal hydride batteries are high cost, high self-discharge and heat generation at high temperatures, and the need to control hydrogen loss.
Battery Recycling
As electric vehicles become more popular, the battery recycling market could grow tremendously. Extensive battery recycling prevents hazardous materials from entering the waste stream, both at the end of the battery life and during manufacturing. The recovery of materials from the recycling process will also introduce important materials into the supply chain and increase the source of this material in the country and the nickel market.
Work is currently underway to develop battery recycling processes to minimize the lifecycle impact of using lithium-ion and other batteries in vehicles. But not all recycling processes are the same and require different separation methods to recover the material:
Smelting: The smelting processes recover the basic elements or salts. These processes are now working on a large scale and can accept several types of batteries, including lithium-ion and nickel-metal hydride. Fusion takes place at high temperatures, where organic materials, including electrolytes and carbon anodes, are burned as fuel or reducing agents. Precious metals are recovered and sent for refining to make the product suitable for all uses. Other materials, including lithium, contained in the slag, are now used as additives in concrete.
Direct Recovery: On the other hand, some recycling processes recover battery feed materials directly. Components are separated by a variety of physical and chemical processes, and all active materials and metals can be recovered. Direct recovery is a low temperature process with minimal energy requirements.
Intermediate Process: The third type of process lies between the two extremes. These processes can accept a wide range of batteries, unlike direct recovery, which recovers the material in the production line rather than smelting it. Separation of different battery materials is often an obstacle in the recovery of high-value materials. Therefore, battery design that takes disassembly and recycling into account is important for electric vehicles to succeed from a sustainability standpoint. Standardizing batteries, materials and cell designs will also make recycling easier and more cost-effective.
With automotive batteries currently being warranted for five to eight years, end-of-life recycling will become big business in the not-too-distant future. In addition, the increasing volume of batteries available for recycling over the medium term will reward investments in new recycling facilities and research into technologies that will increase material recovery efficiency and reduce costs, as that contributes to the creation of a circular economy.
Nickel mining company Hallmark Mining Corporation is poised to meet this global demand for nickel; to find out more, visit our website.
Source: The Nickel Institute