An Insight Into Mining Production and Modern Mining Tools
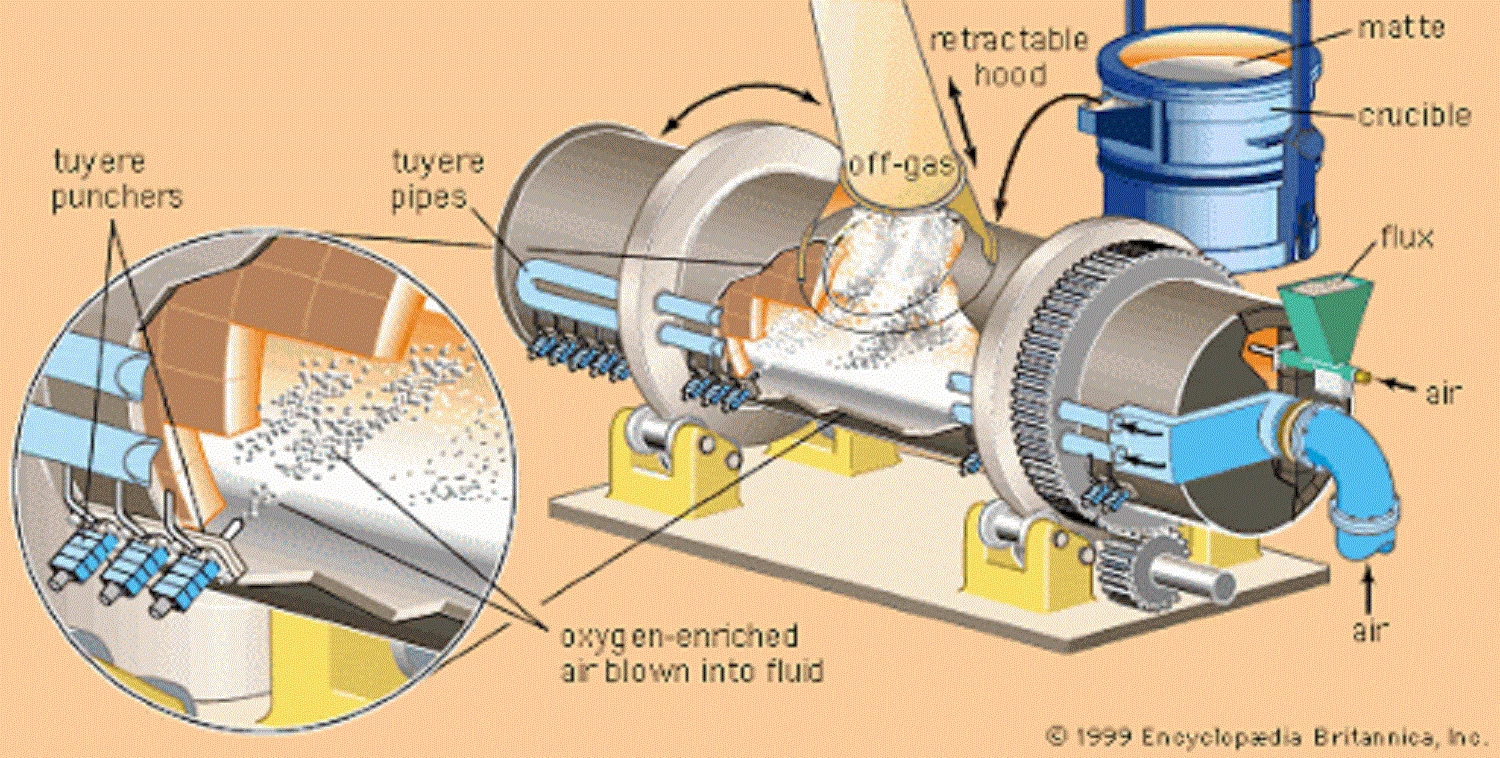
Mineral processing, the practice of preparing raw ores and other materials for extraction of useful constituents while avoiding contamination from impurities known as gangue. Concentration is the initial step in the extraction process in metallurgy, and is performed on most ores using modern mining tools. Comminution and concentration are the backbone of any modern mining production and mineral processing facility, but other vital processes, such as sampling and analysis and dewatering, are also crucial to the industry.
Because of Indonesia's restriction on Nickel ore exports as of the start of 2020, the Philippines has stepped up to become a key provider of Nickel exports. Among the world's largest producers of lateritic Nickel ore is the Philippines. Though its composition is complex, this Nickel ore can be loosely classified as either limonite or silicon-magnesium Nickel. As an added bonus, it may be easily extracted from an open pit and contains just trace amounts of cobalt, sulfur, and calorific value.
Washing the ore, crushing it, screening it, milling it in a ball mill, separating it using magnets and froth flotation, drying it, and finally melting it using mineral processing equipment are all necessary steps in processing laterite Nickel ore. Useful Nickel mineral content can be found in a wide range of ore types. The Philippines mining production BNML limonite with +50mm has a Nickel grade of up to 2.89%, demonstrating that the highest quality minerals are those with the finest grain sizes.
Most laterite Nickel ore may be found in sapropelic deposits, and the Nickel content of laterite increases with depth. There is always some clay and other impurities present with the raw Nickel ore. In order to increase productivity and get a higher quality Nickel concentrate, washing the ore can get rid of the clay and other impurities that would otherwise clog up the crushing and beneficiation processes.
Laterite ore is typically washed using a coarse and fine material screw washer. It's useful for processing lateritic Nickel ore down to -10mm (3/8 inch) in size "at once; simultaneously. Screw washers are superior to conventional ore washing machines because of their ability to recover more fine-sized products from the wash water.
Due to the presence of huge, columnar rocks that have not undergone significant weathering, raw laterite Nickel ore must be crushed before it can be processed. As a result of the modern mining tools, the massive block of Nickel ore would be reduced to a manageable size, reducing the likelihood of the mesh in the screening process becoming blocked.
Nickel ore is best crushed using a cone crusher. The uniform and high quality of the product's particles is a direct result of the lamination crushing principle. The procedure begins with a primary cone crusher decreasing the size of the material to between -5 and -1/2 inches, and then a short head cone crusher reduces the size even further to between -1/2 and -inch "regarding size. The crushing chamber can be adjusted to accommodate a wide range of materials. And maybe most notably, its big head displacement lets more stuff go round and round at once.
Following reduction in size by cone crushers, the Nickel ore is finely processed to a mesh size of -100 using ball mills.
Ores and other raw materials can be ground into a fine powder in a ball mill, which can then be controlled in terms of particle size and utilized to provide uniform flotation feed. The cyclones and particle-size-measuring device form a closed-loop system that ensures only the right-sized particles are sent on to the flotation process.
To obtain pyrrhotite in a separated state, wet magnetic separation is used in mineral processing equipment. When finished, pyrrhotite with a mesh size of -100 will not be suitable for froth flotation and will need to be ground down to -200 in a ball mill before being classified using screens and cyclones.
The next stage is to transmit pyrrhotite that has been crushed to a size of -200 mesh to froth flotation machinery capable of extracting a Nickel concentrate of 3%. The nonmagnetic ore that is left over should be processed in a sequence of rougher, cleaner flotation cells to extract an average of 31% copper concentrate. Finally, the Nickel in the tailings can be recovered by sending them to a second flotation cell, where they will join the existing 3% Nickel concentrate to yield a 12% Nickel concentrate.
Modern mining tools such as rotating drum dryers and kilns are used for drying. Since Nickel ore from the Philippines often has a high moisture content, a drying procedure is essential. Crushed Nickel ore is first dried in a rotary dryer to get rid of the free moisture, and then it's treated in a rotary kiln to get rid of the chemically bound moisture and the oxide component. Pre-reduction is the name for the step in the process. The ultimate goal is to keep the rotary kiln temperature below 800 degrees Celsius, where olivine production is prevented.
Smelting Down to Size As a second step, the Nickel is reduced and smelted in an electric furnace following its treatment in the rotary kiln. Technology that eliminates the need for mixing limestone flux into the crude Nickel-iron in the electric furnace can be implemented to raise the grade to 35%. However, it is essential to pay attention to laterite ore properties, physicochemical reactions in the furnace, and other economic indicators.
When the smelting process was complete, the material would be fed into the rotary cooler at the cylinder's end for immediate cooling. At the opposite end, the finished Nickel product is discharged by showering the material with a cool air stream or spraying water onto the external surface of the cylinder.
Different forms of Nickel ore, cobalt concentration, and the availability of fuel, water, electricity, and chemical reagents are all factors that must be taken into account while planning for the mining production development of Nickel laterite mines.
Hallmark Mining Corporation is a Nickel manufacturer and mining interest in the Philippines with a commitment to sustainable and responsible mining; for more information visit our website.