Automobile Manufacturers Race to Be a Part of the Future of Electric Cars
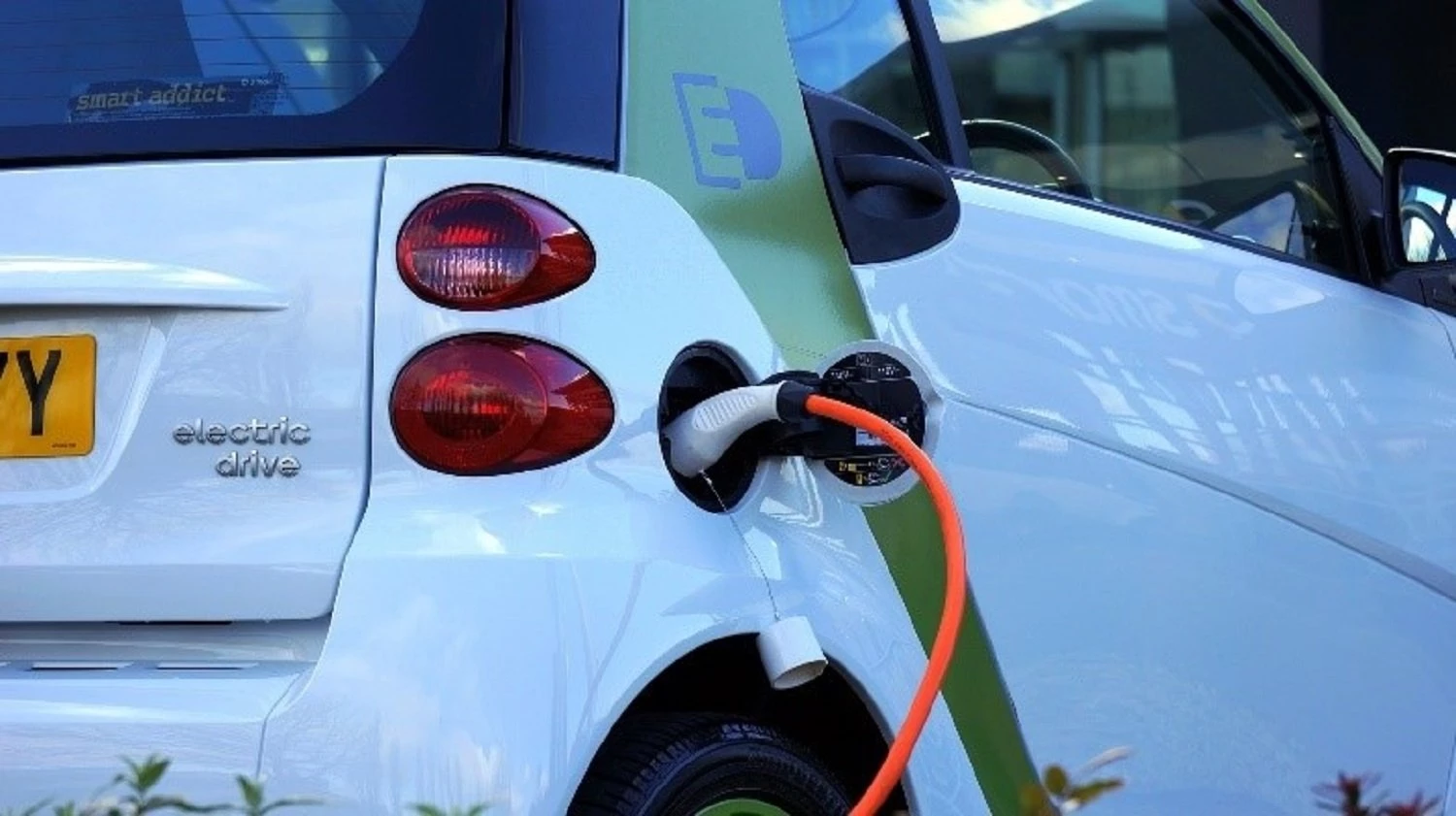
In secret research hubs and (not-so-secret) factories from the United States, Japan, China, and throughout Europe established carmakers all over the planet are tearing up their plans of action in the desire to adjust to another world where power replaces gas and diesel. Factories are being redesigned to deliver electric vehicles, and automakers are stocking up every battery they can find. History is not the best indicator of who will emerge victorious in the emerging battlefield of the electric vehicle or EV. Over the decades automobile manufacturers have had a poor track record with electric vehicles.
General Motors’ EV1 first appeared on American roads in 1996, the same year the auto industry successfully lobbied against a mandate from the California Air Resources Board to make more electric vehicles. The model was canceled in 2003, the effect being a large number of unhappy customers and the release of a conspiratorial documentary ‘Who Killed The Electric Car?’ Chevrolet cancelled production on the Volt, which never sold in significant numbers, sometime in 2018. Nissan’s Leaf remains in production but it has failed to achieve the level of commercial success envisioned by the company’s former chairman, Carlos Ghosn. More broadly, international demand has been hampered by fears over the driving range of the cars, a lack of charging infrastructure, and the significantly higher selling prices for Electric Vehicles.
But all is not doom-and-gloom for the future of electric cars.
The trends in electric cars in transportation is essentially as huge as the change from the pony and buggy to the Model T. In the not-to-distant future – some experts believe as early as 2030 – most of new vehicles being rolled out by automakers will be electric. Development, though, has been fairly slow especially compared to the relative speed in which other technologies such as cellular phones and computers have surged.
What’s to blame? Batteries.
It may appear bizarre but the fact of the matter is that the same carbon and metal oxide-based lithium-particle battery that fueled your Nokia phone in 2004 is basically and exactly the same thing driving each electric vehicle on the market and road today. It is just that electric vehicles use much more of these batteries.
In addition to that, the science within that lithium-particle battery hasn't changed since Sony first presented it on the technology market in 1991. Researchers and designers have endeavored to attempt to make batteries all the more powerful, yet the industry is already hitting the limits of what Lithium-Ion batteries are capable of doing. After more than 20 years of those approaches gaining significant headway, the most recent five years have conveyed only 1% to 2% execution enhancements at regular intervals.
Nickel has transformed into an essential part of lithium-particle battery cathodes as of late, and although current demand in nickel supply for car batteries is only 5%, market research firm Roskill says in another report that utilization in lithium-particle batteries will before long address the second-biggest end-use market for nickel. Meeting the projected flood in nickel request is probably going to require an imaginative, multi-pronged methodology that boosts nickel assets.
The use of nickel in lithium-ion batteries improves the energy density and storage capacity of the batteries. This improved energy density and storage capacity means that the EV can travel more miles on a single charge. This is an important issue for the widespread adoption of EVs – range being one of the much-studied trends in electric cars. Nickel does all this at a relatively low cost. This is a big advantage, as the cost of the battery is also a major impediment to market adoption and is already the primary hindrance to the future of electric cars.
As a result, automakers are using more nickel than ever before. Early generation nickel-manganese-cobalt (NMC) batteries are now the mainstream cathode chemical, starting with about 33% nickel. Nickel content continues to increase in subsequent generations, with the latest generation NMC batteries (NMC 811) approaching 80% of nickel from the world’s nickel manufacturers. It is said that NCM90, which is a 90% nickel cathode, is under development.
There is a real pressure on automobile manufacturers as sulfide deposits for the nickel supply for car batteries become increasingly difficult to obtain, the nickel manufacturer will have to explore all options and it is encouraging that several new projects are underway. However, it is unlikely that significantly increased nickel production will come online soon, as the road to production is known to be long.
Some in the industry believe that the lack of Class 1 resources may facilitate further development to improve the economics of processing laterite nickel ore such as those at the Pujada Nickel Project of nickel manufacturer Hallmark Mining Corporation. Many expect high-pressure acid leaching (HPAL) to dominate this market, but the technology still presents some challenges, leaving the door open for further advances in other technologies.
Ultimately, no one knows what the nickel industry will look like in the future, but rising demand for lithium-ion batteries - and trends in electric cars - could radically change the nickel market. Taking advantage of all the opportunities for battery grade nickel, from new capacities to recycled metals, is important to meet demand.
Hallmark Mining Corporation is a nickel mining company in the Philippines. To find out more visit our Pujada Nickel Project
Sources: CNN Business, Feeco International, Bloomberg